Laser cleaning: A solution for removing contaminants from 3D-printed objects.
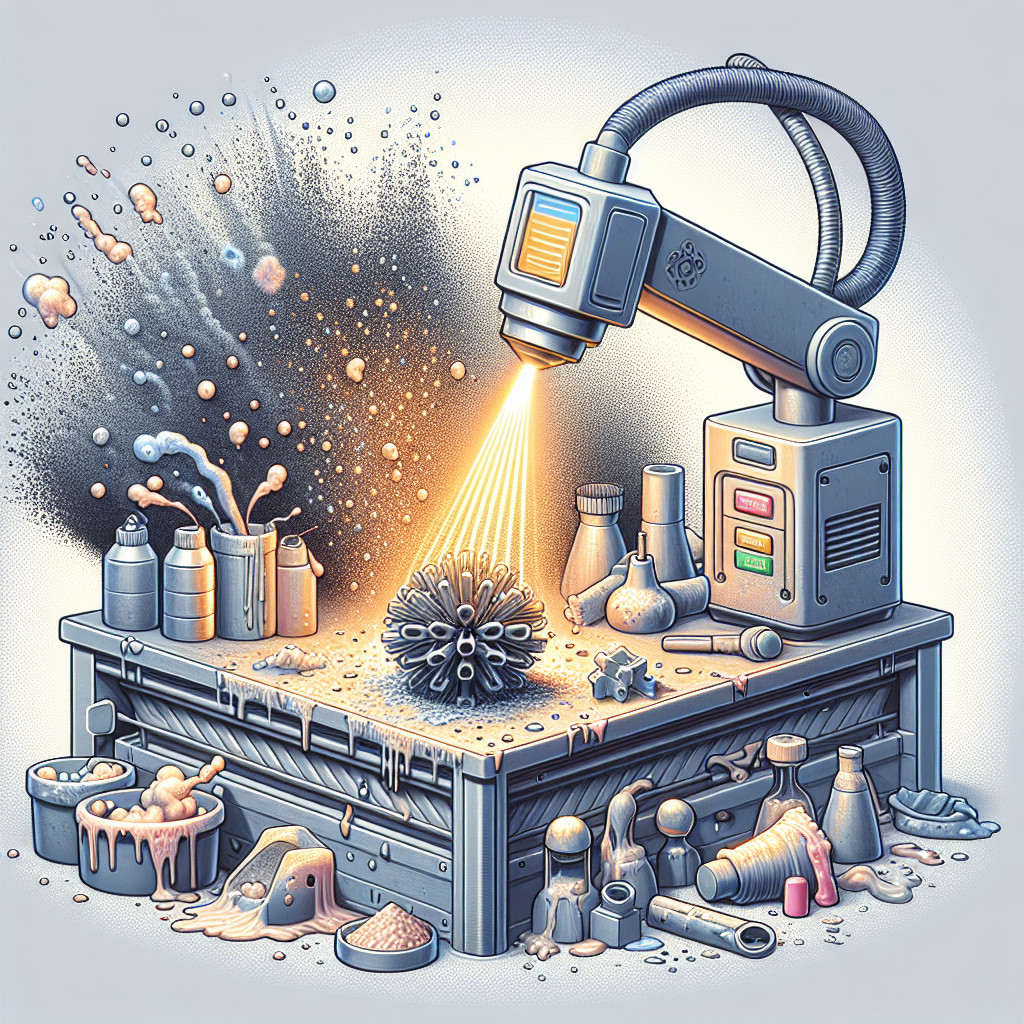
- Overview of 3D printing technology
- Cost-effectiveness of laser cleaning for 3D-printed objects
- Impact of laser cleaning on the 3D printing industry
- Regulatory requirements for using laser cleaning technology
- Collaborations between 3D printing and laser cleaning companies
- Comparison of different types of lasers used for cleaning 3D-printed objects
- Challenges of removing contaminants from porous materials using laser cleaning
- Cost-effectiveness of laser cleaning for 3D-printed objects
Overview of 3D printing technology
3D printing technology has revolutionized the way we manufacture products, allowing for faster prototyping, customization, and cost-effective production. This article will provide an overview of the key aspects of 3D printing technology, including its history, applications, and future potential.
History of 3D printing
The concept of 3D printing dates back to the 1980s when Chuck Hull invented stereolithography, a process that uses UV light to solidify liquid resin layer by layer. Since then, 3D printing technology has evolved rapidly, with new materials and techniques being developed to create complex and functional objects.
Applications of 3D printing
3D printing technology is used in a wide range of industries, including aerospace, automotive, healthcare, and consumer goods. In aerospace, 3D printing is used to create lightweight and durable parts for aircraft and spacecraft. In healthcare, 3D printing is used to create custom implants, prosthetics, and medical devices. In consumer goods, 3D printing is used to create personalized products and prototypes.
Future potential of 3D printing
The future of 3D printing technology looks promising, with advancements in materials, speed, and scale. Researchers are exploring new materials such as biodegradable plastics and metal alloys for 3D printing. They are also developing faster printing techniques, such as continuous liquid interface production (CLIP) and selective laser sintering (SLS). Additionally, companies are exploring the potential of large-scale 3D printing for construction and infrastructure projects.
In conclusion, 3D printing technology has the potential to revolutionize manufacturing and design processes across industries. With ongoing advancements in materials and techniques, 3D printing is poised to become a mainstream manufacturing technology in the near future.
#3Dprinting #technology #manufacturing #innovation #prototyping #customization #futurepotential
frazy kluczowe:
– 3D printing technology applications in healthcare
– Advancements in 3D printing materials
– Future of large-scale 3D printing
– 3D printing technology in aerospace industry
– Customization and personalization in 3D printing
Cost-effectiveness of laser cleaning for 3D-printed objects
One promising solution to this problem is laser cleaning, a non-contact and environmentally friendly method that uses high-energy laser beams to remove contaminants from the surface of objects. Laser cleaning has been shown to be highly effective for cleaning 3D-printed objects, offering advantages such as precision, speed, and minimal material waste.
But is laser cleaning cost-effective for 3D-printed objects? 馃
Several studies have investigated the cost-effectiveness of laser cleaning compared to traditional cleaning methods such as manual labor or chemical baths. These studies have found that while the initial investment in laser cleaning equipment may be higher, the long-term savings in labor costs, material waste, and environmental impact can make laser cleaning a more cost-effective option in the long run.
Additionally, laser cleaning can improve the quality and consistency of cleaning results, reducing the risk of defects and rework in the manufacturing process. This can lead to further cost savings by minimizing scrap and improving overall production efficiency.
In conclusion, laser cleaning offers a cost-effective and efficient solution for cleaning 3D-printed objects, providing benefits such as precision, speed, and environmental sustainability. As the technology continues to advance and become more widely adopted, laser cleaning is likely to play an increasingly important role in the post-processing of 3D-printed objects.
Hashtags: #3Dprinting #laserCleaning #costEffective #manufacturing #technology
Keywords: laser cleaning, 3D printing, cost-effectiveness, manufacturing, post-processing
Long-tail phrases: cost-effective laser cleaning for 3D-printed objects, advantages of laser cleaning in manufacturing, environmental benefits of laser cleaning.
Impact of laser cleaning on the 3D printing industry
The is significant. Here are some of the key benefits:
馃敼 Improved efficiency: Laser cleaning can significantly reduce the time and effort required for post-processing, allowing manufacturers to increase their production capacity and meet tight deadlines.
馃敼 Enhanced precision: The precise control offered by laser cleaning ensures that only the targeted material is removed, minimizing the risk of damage to the printed part.
馃敼 Eco-friendly: Unlike chemical cleaning methods, laser cleaning does not produce any harmful waste or emissions, making it a more sustainable option for manufacturers.
馃敼 Cost-effective: While the initial investment in laser cleaning equipment may be higher than traditional cleaning methods, the long-term savings in labor and material costs can make it a more cost-effective solution.
Overall, laser cleaning has the potential to revolutionize the 3D printing industry by streamlining the post-processing workflow and improving the quality of printed parts. As the technology continues to evolve and become more accessible, we can expect to see even greater advancements in the field of additive manufacturing.
#3Dprinting #laser cleaning #manufacturing #technology #post-processing
frazy kluczowe:
– laser cleaning in 3D printing
– benefits of laser cleaning
– impact on manufacturing industry
– precision in post-processing
– eco-friendly cleaning solution
Regulatory requirements for using laser cleaning technology
Occupational Safety and Health Administration (OSHA)
One of the primary regulatory bodies overseeing the use of laser cleaning technology is the Occupational Safety and Health Administration (OSHA). OSHA sets forth guidelines for the safe operation of lasers, including proper training for workers, the use of personal protective equipment, and the implementation of safety protocols to prevent accidents and injuries.
Environmental Protection Agency (EPA)
The Environmental Protection Agency (EPA) also plays a role in regulating the use of laser cleaning technology. The EPA monitors emissions from laser cleaning equipment to ensure compliance with air quality standards and prevent the release of harmful pollutants into the environment.
International Organization for Standardization (ISO)
The International Organization for Standardization (ISO) has developed standards for laser safety, including ISO 11553 which specifically addresses the safety requirements for laser cleaning systems. Compliance with ISO standards is essential for ensuring the safe and effective use of laser cleaning technology.
Personal Protective Equipment (PPE)
Workers using laser cleaning technology must wear appropriate personal protective equipment, such as safety glasses, gloves, and protective clothing, to prevent exposure to laser radiation and hazardous materials. Employers are responsible for providing and enforcing the use of PPE to protect their workers.
Training and Certification
Proper training and certification are essential for workers operating laser cleaning equipment. Training programs should cover the safe use of lasers, hazard identification, emergency procedures, and maintenance protocols. Certification ensures that workers have the knowledge and skills to operate laser cleaning technology safely and effectively.
- Compliance with regulatory requirements is essential for the safe and effective use of laser cleaning technology.
- Regulatory bodies such as OSHA, EPA, and ISO set forth guidelines for the operation of laser cleaning equipment.
- Workers must receive proper training and certification to operate laser cleaning technology safely.
- Personal protective equipment is necessary to prevent exposure to laser radiation and hazardous materials.
- Occupational Safety and Health Administration (OSHA)
- Environmental Protection Agency (EPA)
- International Organization for Standardization (ISO)
- Personal Protective Equipment (PPE)
- Training and Certification
#laser cleaning technology, regulatory requirements, OSHA, EPA, ISO, personal protective equipment, training and certification
#safe operation, environmental impact, occupational safety, laser safety standards, hazard identification, emergency procedures, maintenance protocols
Collaborations between 3D printing and laser cleaning companies
Benefits of collaboration
– Improved quality of 3D printed parts: Laser cleaning can be used to remove impurities and imperfections from 3D printed parts, resulting in higher quality and more reliable products.
– Increased efficiency: By combining 3D printing and laser cleaning technologies, manufacturers can streamline their production processes and reduce the time and resources required to produce parts.
– Cost savings: can lead to cost savings through improved efficiency, reduced waste, and lower maintenance costs.
– Environmental sustainability: Laser cleaning is a non-contact and environmentally friendly process that does not produce any waste or harmful emissions, making it a sustainable alternative to traditional cleaning methods.
Examples of successful collaborations
– A leading 3D printing company has partnered with a laser cleaning company to develop a new system that integrates both technologies, allowing for the in-line cleaning of 3D printed parts during the manufacturing process.
– Another collaboration between a 3D printing company and a laser cleaning company has resulted in the development of a specialized cleaning solution for metal 3D printed parts, ensuring optimal surface quality and performance.
Future prospects
The collaboration between 3D printing and laser cleaning companies is expected to continue growing in the coming years, as manufacturers increasingly recognize the benefits of integrating these technologies. This trend is likely to lead to the development of new and innovative solutions for a wide range of industries, from aerospace and automotive to healthcare and consumer electronics.
In conclusion, have the potential to revolutionize the manufacturing industry and drive innovation in product design and production. By leveraging the strengths of both technologies, manufacturers can achieve higher quality, increased efficiency, and cost savings, while also contributing to environmental sustainability.
#3Dprinting #lasercleaning #manufacturing #innovation #collaboration
frazy kluczowe:
– benefits
– Successful examples of
– Future prospects of
Comparison of different types of lasers used for cleaning 3D-printed objects
Types of lasers
There are several types of lasers that can be used for cleaning 3D-printed objects, each with its own advantages and limitations. The most common types of lasers used for cleaning include:
Laser Type | Wavelength | Power | Advantages | Limitations |
---|---|---|---|---|
CO2 Laser | 10.6 碌m | High | Effective for organic materials | Not suitable for metals |
Fiber Laser | 1.06 碌m | High | Good for metals | Less effective on plastics |
UV Laser | 355 nm | Low | High precision | May damage sensitive materials |
Comparison
When comparing different types of lasers for cleaning 3D-printed objects, it is important to consider factors such as the type of material being cleaned, the level of precision required, and the potential for damage to sensitive materials. CO2 lasers are effective for organic materials but may not be suitable for metals, while fiber lasers are good for metals but less effective on plastics. UV lasers offer high precision but may damage sensitive materials.
Conclusion
In conclusion, the choice of laser for cleaning 3D-printed objects will depend on the specific requirements of the cleaning process. CO2 lasers, fiber lasers, and UV lasers each have their own advantages and limitations, and the best choice will depend on the material being cleaned and the desired level of precision. By carefully considering these factors, manufacturers can select the most suitable laser for cleaning their 3D-printed objects.
#laser #cleaning #3Dprinting #manufacturing #CO2laser #fiberlaser #UVlaser #precision #materials
frazy kluczowe:
– comparison of different types of lasers
– lasers used for cleaning 3D-printed objects
– advantages and limitations of laser cleaning
– choosing the right laser for cleaning 3D-printed objects
Challenges of removing contaminants from porous materials using laser cleaning
One of the main challenges of using laser cleaning on porous materials is the risk of damaging the material itself. Porous materials have a complex structure with interconnected voids and channels, which can make it difficult for the laser beam to penetrate deeply enough to remove contaminants without causing damage. Additionally, the high energy of the laser beam can cause thermal damage to the material, leading to cracks or other forms of degradation.
Another challenge is the uneven distribution of contaminants within the porous material. Contaminants can be trapped deep within the pores, making it difficult for the laser beam to reach and remove them effectively. This can result in incomplete cleaning and the recontamination of the material shortly after the cleaning process.
Furthermore, the type of contaminants present on porous materials can also pose a challenge. Some contaminants may be more resistant to laser cleaning than others, requiring higher energy levels or longer exposure times to remove effectively. Additionally, certain contaminants may react with the material or the laser beam itself, leading to the formation of harmful byproducts.
Despite these challenges, laser cleaning can still be a highly effective method for removing contaminants from porous materials when used correctly. By adjusting the laser parameters, such as energy level, pulse duration, and spot size, it is possible to optimize the cleaning process and minimize the risk of damage to the material. Additionally, using specialized laser systems with scanning capabilities can help to ensure uniform cleaning of the entire surface.
In conclusion, removing contaminants from porous materials using laser cleaning presents several challenges, including the risk of damaging the material, uneven distribution of contaminants, and the type of contaminants present. However, with careful optimization of laser parameters and the use of specialized laser systems, it is possible to overcome these challenges and achieve effective cleaning results.
#laser #cleaning #contaminants #porousmaterials #challenges
frazy kluczowe:
– challenges of laser cleaning porous materials
– removing contaminants from porous surfaces
– optimizing laser parameters for porous materials
– effective cleaning of porous materials using laser technology
Cost-effectiveness of laser cleaning for 3D-printed objects
The cost-effectiveness of laser cleaning for 3D-printed objects lies in its efficiency and precision. Traditional cleaning methods, such as manual sanding or chemical baths, can be labor-intensive and time-consuming. Laser cleaning, on the other hand, can be automated and completed in a fraction of the time, saving on labor costs and increasing productivity.
Benefits of laser cleaning for 3D-printed objects:
- Efficiency: Laser cleaning is a fast and efficient process, reducing the time needed for post-processing.
- Precision: The laser can target specific areas on the object, ensuring a thorough cleaning without damaging the surface.
- Cost-effectiveness: While the initial investment in a laser cleaning system may be high, the long-term savings on labor and materials make it a cost-effective solution.
- Environmentally friendly: Laser cleaning does not require the use of harsh chemicals, making it a more sustainable option for cleaning 3D-printed objects.
Conclusion
Laser cleaning is a cost-effective and efficient solution for cleaning 3D-printed objects. Its precision and speed make it a valuable tool for manufacturers looking to streamline their post-processing operations. While the initial investment may be high, the long-term savings and benefits of laser cleaning make it a worthwhile investment for businesses in the 3D printing industry.
#laser #cleaning #3Dprinting #costeffectiveness #efficiency #precision #environmentallyfriendly #manufacturing
frazy kluczowe:
– benefits of laser cleaning for 3D-printed objects
– cost-effective solutions for post-processing
– environmentally friendly cleaning methods for manufacturers
- Mobile applications versus web applications. How are they different? - 30 August 2024
- Laser cleaning: A solution for removing contaminants from 3D-printed objects. - 3 April 2024
- Chatbots and the benefits of implementing them - 4 January 2024